Engineered Solutions
Vacuum Belt Conveyors
Vacuum Conveyors
Vacuum Belt Conveyors
Among all of your conveying options, vacuum belt conveyors are ideal when you’re working with small, flat parts and other lightweight, thin materials. Like all Dorner conveyor solutions, our vacuum belt conveyors come in a variety of configurations, enabling you to optimize your physical space while keeping your production and budget needs in mind. Some models handle varying elevations, enabling you to fit them into tight spaces. Additionally, a range of add-ons and accessories help meet your product and process needs. See vacuum conveyor belt technology in action in this video showing small packaged goods running on the underside of a conveyor.
How Do Vacuum Conveyors Work?
Vacuum conveyors work by creating suction that keeps items flat on the belt surface. For example, a vacuum conveyor belt could prevent sheets of paper, plastic parts, cardboard, leaflets, small pouches, or empty plastic packaging from flying away as they move down the line.
This suction power is created by an internal vacuum pump that pulls air flows through perforations within the belt. This creates a seal, keeping items intact.
Each vacuum conveyor is custom designed based on the customer’s application and product. Dorner’s engineers work with our customers to figure out the proper belt and hole spacing, pattern and size.
Vacuum conveyors use a custom bed plate with a vacuum chamber to focus the suction on the proper place. Ports are custom-drilled into the conveyor frame for the vacuum. The number of ports drilled depends on our customers’ needs.
There is no vacuum on the conveyor tails. The suction prevents any slipping or sliding of the product while the product can still be easily lifted away from the belt.
Dorner can provide the blower assembly or our customers can provide their own.
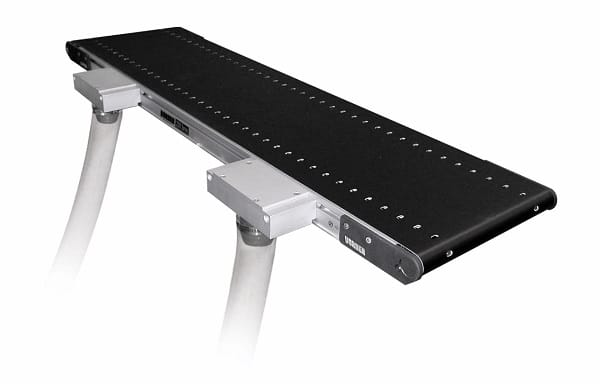
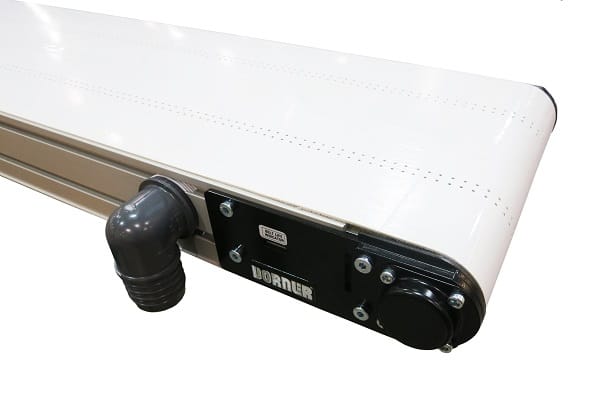
Vacuum Conveyor Applications
Vacuum conveyors are seen in a variety of industries, from health care and pharmaceuticals to manufacturing and metalworking. Within these and other industries, vacuum conveyors are useful for many specific applications, including:
- Inspection
- Precision part movement
- Small part handling and positioning
- Work holding
- Part and package infeed and outfeed
- Printing
- Automated assembly
- Manual assembly
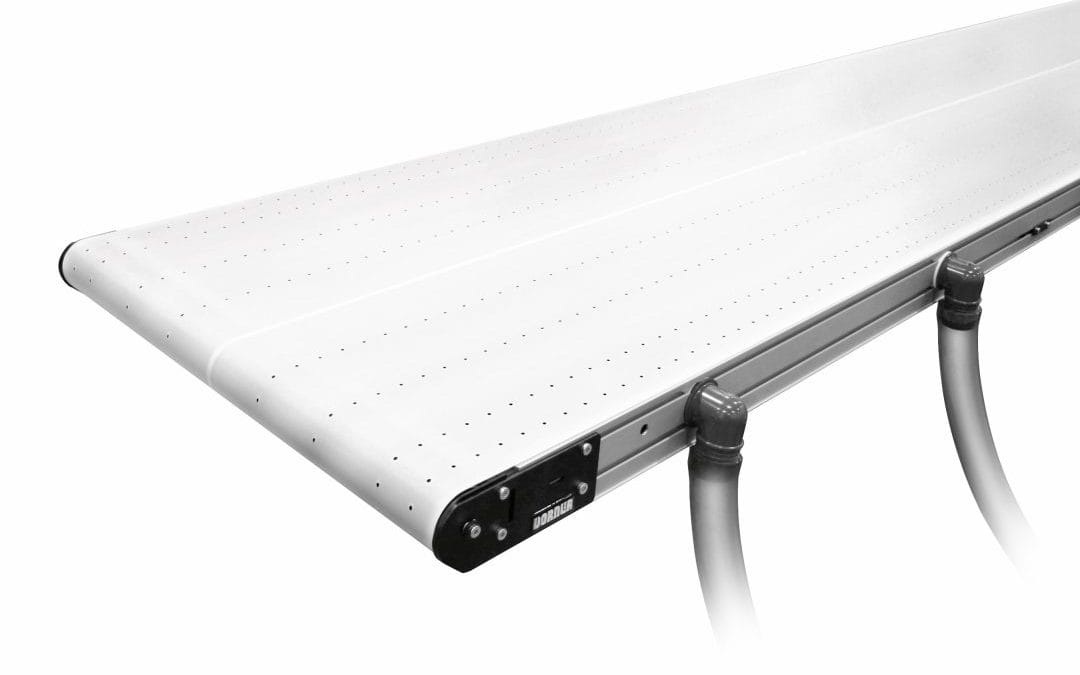
Custom Vacuum Conveyors
Sometimes an out-of-the-box solution isn’t enough for your unique products, applications, or business goals. A leading vacuum conveyor manufacturer, Dorner is also home to our seasoned Engineered Solutions Group. This full-service team can modify a standard solution to meet your needs, or can collaborate with you to build a completely custom system. We work with you from concept to completion, including a full needs analysis, CAD modeling, mechanical design and other aspects of the custom vacuum conveyor design process.
Vacuum Conveyor Design
Dorner’s vacuum conveyor design experts find solutions to meet each customer’s exact part-moving needs. We combine our vacuum belt conveyors with expert control technology to ensure precision part location, whether it’s fluting paper, empty plastic bottles or injection-molded parts. Our custom vacuum conveyors are also built to fit into a variety of spaces, and they can be integrated with a wide range of accessories.
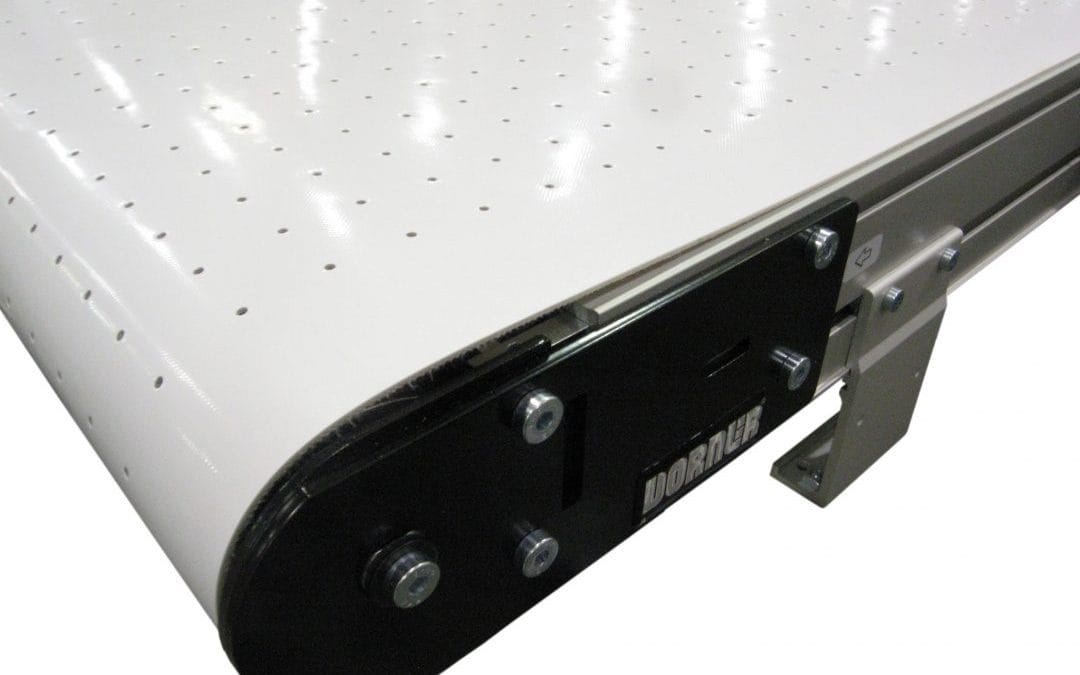
Vacuum Conveyor Belt Systems
Dorner offers a variety of durable, high-quality vacuum conveyor belt systems for our 2200 and 3200 series.
2200 Series Vacuum Conveyor
Dorner’s 2200 Series conveyors work best for small to medium part handling. These systems can handle loads up to 120 pounds and speeds up to 400 feet per minute. This specs and capabilities of the 2200 vacuum belt conveyor systems fit the needs of the pharmaceutical and medical industries well.
3200 Series Vacuum Conveyor
Our 3200 Series conveyors line is ideal for long runs, high speeds and heavier loads. Suitable applications include part handling and accumulation, processing and packaging, automation and assembly. This system has flexible layout options, with the ability to handle inclines and declines.
Features & Specifications
Our vacuum conveyors and belts can be configured in a variety of ways. Here is a look at standard features and specifications:
- Available on Dorner industrial conveyor platforms.
- End and center drive compatible.
- Rack and pinion belt tensioning.
- Sealed ball bearings.
- Vacuum source is provided by a regenerative vacuum blower.
- Standard belting is recommended.
- V-guided and non-V-guided belt compatible.
- Friction belting is available for rigid parts like plastic caps, plastic bottles, ceramic wafers, glassware, etc.
- Electrically conductive belting is available for thin products such as paper, light cardboard, cloth, plastic film, etc.
You can reference specific conveyor specification sheets for additional details or contact one of our representatives for more information.
Accessories & Customizations
Our vacuum belt conveyor systems work with a variety of accessories, support stands, gearmotors and mounting packages. Examples options include:
- Light-duty, standard-duty or heavy-duty gearmotors.
- Side, bottom or top mounts.
- Fixed and adjustable height stands, including a quick-adjust option.
Additionally, the vacuum area of each system is custom-designed for your desired application.
In-House Vacuum Belt Production
All vacuum belts are made at Dorner facilities to ensure optimum part-holding ability and perforation pattern quality. Our qualified team oversees all quality assurance, and this means more-reliable vacuum conveyors and systems for the customer.
Our 140,000-square-foot facility uses lean production techniques, which allows us to design, build and deliver custom vacuum conveyors and other engineered solutions with reduced lead time. Many of our solutions can be delivered within five days.
As with other standard belts, our vacuum belts are run through a drill punch machine, where the holes are created. Every vacuum belt is custom-created. The machine is programmed with the specific length, hole size, hole spacing, etc. This ensures everything is created to the exact specifications needed for our customer’s unique application. The drill punch machine has a wide range of sizes that it can create, so almost all vacuum belts are able to be created in-house.
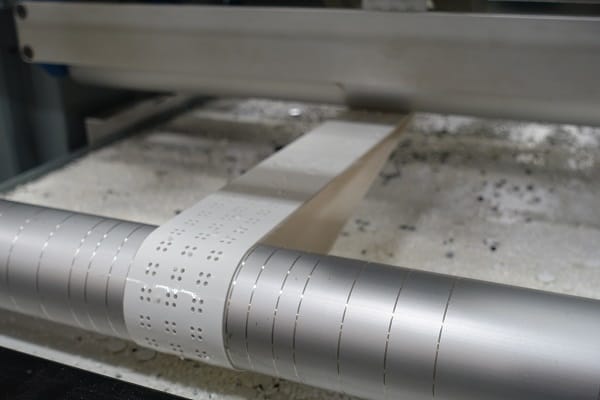
Vacuum Conveyor Manufacturers
Among vacuum conveyor manufacturers, Dorner is the largest supplier of vacuum belts in the industry. Our products are engineered and tested to ensure optimal performance. We stand by our designs and offer a 10-year warranty.
Dorner’s expert sales staff is highly trained in conveying products and technology as well as industry applications. Our team uses this knowledge to help our customers find solutions to their business challenges.
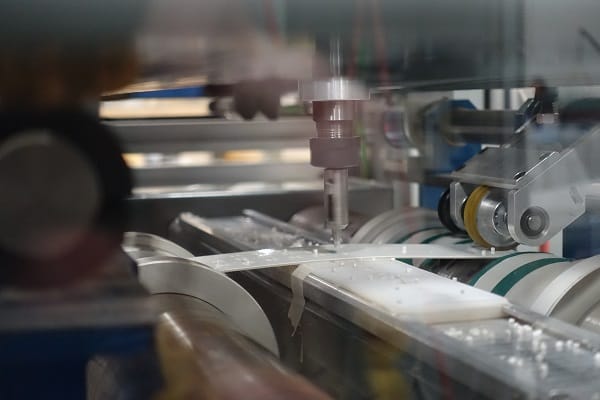
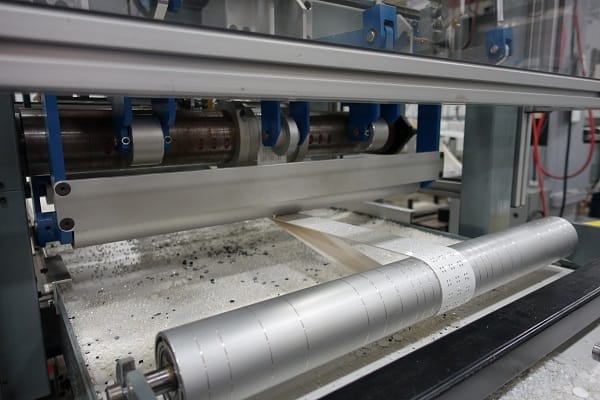
Vacuum Conveyor Installation Services
Dorner is not only a leading conveyor manufacturer but a top vacuum belt conveyor installation company. We’ll send our engineering experts to your location to ensure your equipment is optimized for efficient performance. Our expert vacuum conveyor installation service includes delivery, staging, setup and training.
If you plan to handle installation internally or hire an outside contractor.
Dorner service team member to serve as an on-site supervisor.
Vacuum Conveyor Maintenance Program
Dorner offers a conveyor belt maintenance program in two tiers: labor plus parts and labor. With a focus on preventative maintenance, this service begins with an on-site evaluation of your vacuum conveyor system. After we assess your needs, we’ll create a custom plan that includes our recommended service intervals.
Our vacuum conveyor training services can be done in groups or one-on-one, and it can take place during installation or down the line. After and between training sessions, your team will have 24/7 access to a wealth of online resources such as videos and guides.
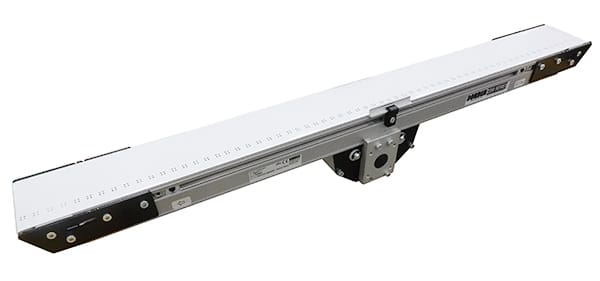
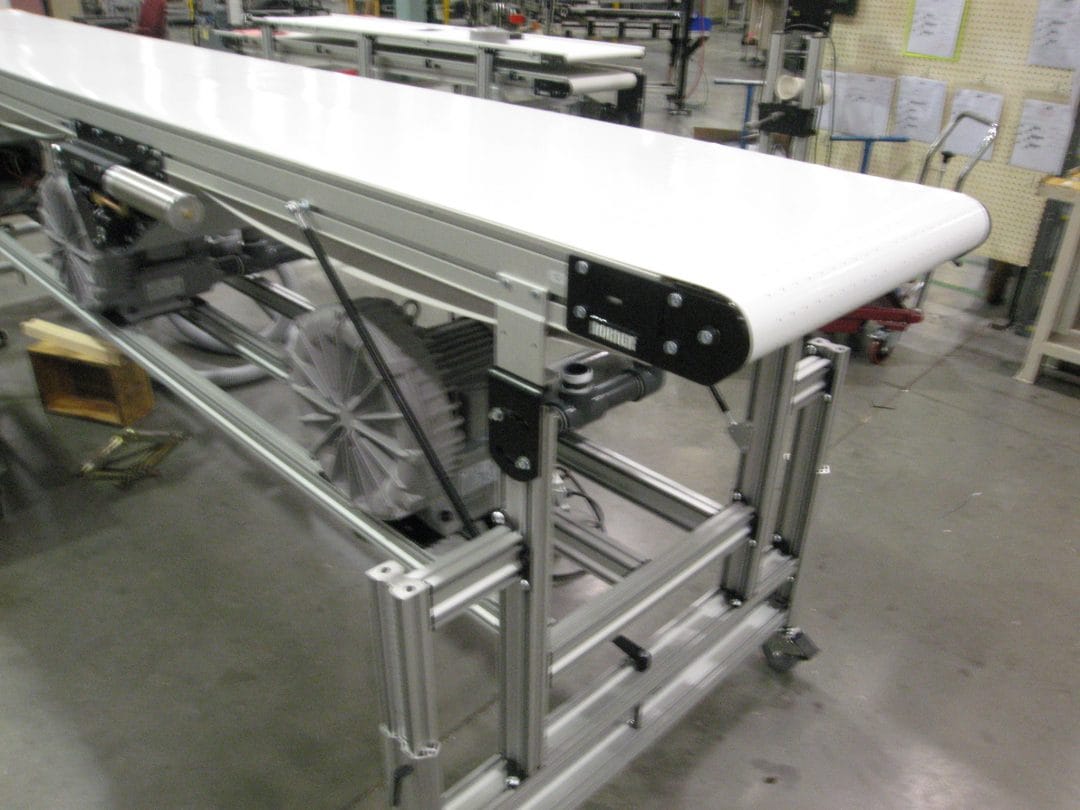
Vacuum Conveyor Installation Services
Dorner is not only a leading conveyor manufacturer but a top vacuum belt conveyor installation company. We’ll send our engineering experts to your location to ensure your equipment is optimized for efficient performance. Our expert vacuum conveyor installation service includes delivery, staging, setup and training.
If you plan to handle installation internally or hire an outside contractor.
Dorner service team member to serve as an on-site supervisor.